Making magic: What goes into creating an award-winning design?
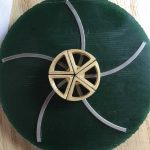
At the bench
While the gems are similar in size and proportion, they vary slightly, especially in depth due to their individual refractive indices influencing the specific pavilion angles. Instead of surface modelling five unique gems, I create a single model that’s an average of the five gems. Next, the bezels are surface modelled and modified as necessary to ensure they form a complete circle when oriented at the pendant’s centre.
Once the gems and bezels are created, I have to figure out how to ensure the five platinum tracks will be consistent and have identical arcs, so the gemstones will move evenly. With experimentation, I decide a circle with a diameter of 65 mm (2.6 in.) will, when cut into five segments, provide a suitable arc for the tracks. I model these in CAD and initially consider having the tracks milled directly from the CAD file then cast in the cobalt-platinum. However, this will be more costly, as I’d have to purchase the extra platinum required for sprues and button.
More critically, however, is the possibility of the platinum tracks, which are extremely malleable after casting, deforming during finishing and diamond setting, losing their vital accuracy. So, I opt to mill 3 sq. mm (0.12 in.) platinum-cobalt wire down to 2 sq. mm (0.08 in.) without annealing, bend it into the 65-mm (2.6-in.) diameter circle, and laser-weld the seam. Careful use of a hammer and round section steel bracelet mandrel ensure the circle is true. The resultant component is then cut into five equal sections.To ensure the precise assembly of the segments, I go back to CAD and use the virtual model of the assembled track as a cutter to Boolean-subtract a corresponding recess from a solid block. This block is then milled and used as a jig to support the five pieces of track with the fabricated bezel for the opal oculus at the centre. The wax jig allows for perfect alignment of the tracks while they are laser-welded together.
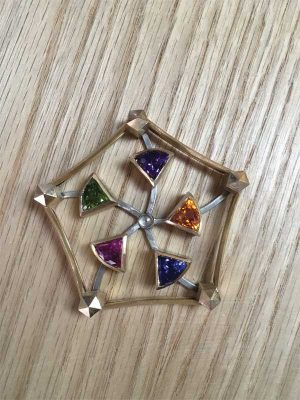
The main yellow gold frame is then milled in two halves, cast, polished, and assembled. The undersides of the five pentagonal terminals are left open and notched to allow the extremities of the five tracks to be slotted in. Next, the platinum tracks are bead-set with the half-point diamonds, and the five coloured gemstones are slid over their rail. The entire assembly is fit into the frame and laser-welded in place.
To finish the back of the piece, I modelled five pentagonal plates to cover the back of the terminals. These incorporated the five alchemical symbols for the elements with the addition of my trademark and quality stamps. The back plates for the five pie-shape bezels are to hold small rare earth magnets on their interior surface. The outside has embossed geometrical representations of the platonic solids for the five elements.
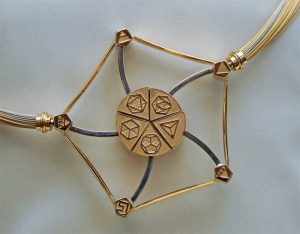
This step is where I ran into problems due to the severe time constraints I was under, as a result of the changed theme. It was not discovered until after the back plates were attached, with their rare earth magnets inserted, that the magnets were not quite strong enough to hold the combined weight of the gems and their bezels in place as planned. It was too late to do anything, so the piece was given its final polish and shipped to Germany to meet the competition deadline.
My finished design is not quite as magical as I had intended, but I know it’s possible to modify the back plates to hold more magnets—that is, of course, when it comes back from its grand European tour.
Always worth it in the end
As I’d hoped, the pentagram worked its magic. This October, my design entry placed third out of 55 entries—the only North American winner!

I want to encourage my fellow designers, and aspiring designers, to keep an eye out for future competition announcements; perhaps more Canadian designers will be on the winner’s podium next time?
Llyn L. Strelau is the owner of Jewels by Design in Calgary. Established in 1984, his by-appointment atelier specializes in custom jewellery design for local and international clientele. Strelau has received numerous design awards, including the American Gem Trade Association’s (AGTA’s) Spectrum Awards and De Beers’ Beyond Tradition—A Celebration of Canadian Craft. His work has also been published in Masters: Gemstones, Major Works by Leading Jewelers. Strelau can be reached via e-mail at designer@jewelsbydesign.com.